Kwik-PDU (Pattern Display Unit)
Can save mining industry millions
By superimposing a drill pattern onto the rock face with a press of a button
NOTE: Kwik-PDU can only do 6m x 6m tunnels
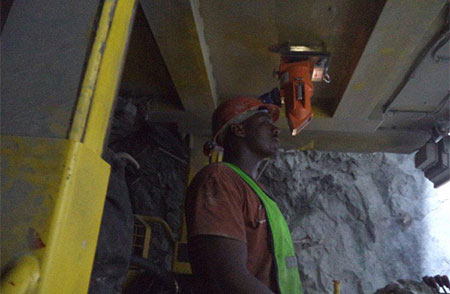
The KWIK-PDU (Pattern Display Unit) will revolutionize the marking off of tunnels in development ends
The first production batch underwent severe shock, vibration, temperature, humidity, water and salt spray testing and all passed with flying colours.
Utilising the same principle employed on a fighter aircraft, where a predetermined as well as a changing pattern, is projected in front of the pilot’s eyes. The KWIK-PDU provides a precise pattern indication for drilling, which ensures face holes which are accurately indicated. (Superimposed). This process to develop and improve this product took years to perfect.
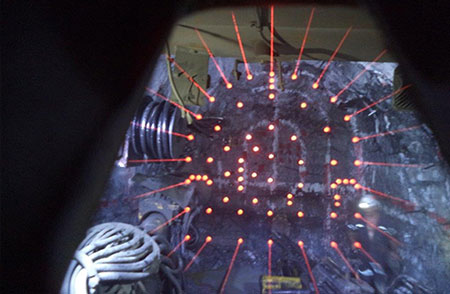
Traditionally, the rock face to be blasted has always been marked with a paintbrush or spray can with the disadvantage of inaccuracy, waste of paint and more importantly – TIME.
With the use of Kwikmark's specially developed and designed software, this allows any given drill pattern to be converted onto a Gradicule ® used within the KWIK-PDU.
These patterns vary from mine to mine and are normally designed or verified by the mines Blasting Engineer who also take into account the need to eliminate secondary blasting, strength of hanging-wall, rock-breaking patterns etc. Different patterns can be made for different applications.
DRILL PATTERN (Gradicule) (Patent No 2016/08591)
The KWIK-PDU is compact and easy to use. It can be used with less than one hour of training, once it is fitted to the clamping bracket on the canopy of any drill rig. The Drill Rig Operator then ensures that the correct Gradicule® is inserted into the KWIK-PDU which he then lines up with direction and grade lines on the rock face and locks it into position to prevent movement during the drilling operation.
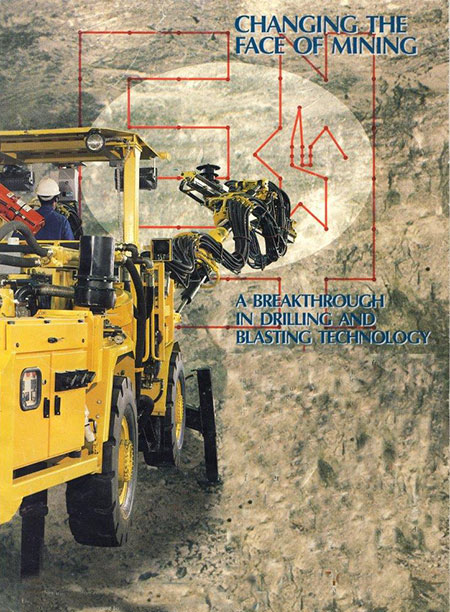
After a short visit to India in 2014 we saw the opportunity to solve the problem in the Hindustan Zinc mines near Jaipur. The KWIK-PDU was the answer to their problem and this technology can be used throughout the world.
Note: By using different coloured Perspex filters, the drill holes and direction lines can be changed to different colours when inserted into the KWIK-PDU.
After the blast holes have been drilled by the Rig Operator, the miner may verify their positioning by viewing the pattern through the KWIK-PDU. Typical accuracies obtained are holes which are less than 50mm away from their intended positions. This results in controlled over break and leads to improved haulage advancement and reduces clearing time.
Since no physical marking of the rock is required, a time saving of up to 45 minutes is gained, which allows for improved underground activity management and supervision.
Scaling of the rock face during the drilling operation does not result in the loss of portions of the indicated drilling pattern. Due to controlled breaking by means of consistent patterns, socket lengths after blasting, are also minimised.
The lightening system uses 1 x AAA rechargeable battery. At a drilling distance of 9m (from cab to rock face) will cover a rock face area of 6m high by 6m wide when using a single pattern.